Upcoming Lean Six Sigma Green Belt Training
Dates | Times | Duration | |
---|---|---|---|
19 & 20 April 2025 | 9:30 AM - 5:30 PM (IST) | 16 Hours | |
17 & 18 May 2025 | 9:30 AM - 5:30 PM (IST) | 16 Hours |
OVERVIEW
Lean Six Sigma is a methodology that relies on a collaborative team effort to improve performance by systematically removing waste.
A defect is defined as failure of a product, process or service in meeting requirements of internal or external customers.
“The Six Sigma” shows the organization’s ability of highly capable processing in producing the outputs within the limited specifications.
Therefore, it can be said that the processes that operates with the Six Sigma quality, is able to produce a quality products at a low rate of defects.
Six Sigma approach is being widely used all over the world for reduction in process variation and waste elimination.
COURSE OUTLINE
The “Lean Six Sigma Green Belt” training is based on international syllabus. The training is very high quality and so precise that we provide 100% pass guarantee in certification exam. In case you do not pass exam we will return your full fee.
UNIT 1: INTRODUCTION & OVERVIEW
Introduction, What is Lean Six Sigma, Six Sigma benefits for individual and organizations, Six Sigma Philosophy, DMAIC overview, Six Sigma Roles & Responsibilities
UNIT 2: DEFINE
The Define phase introduction, Define CTQ, Identify & Analyse customer, Prepare Charter, Documenting existing processes, Team development
UNIT 3: MEASURE
The Measure phase introduction, Detailed process map, Concept of X & Y, Data identification, FEMA and Fishbone analysis, Data collection plan development, Measurement system analysis, Measuring variation and Sigma level calculations
UNIT 4: ANALYZE
The Analyze phase introduction, Process analysis, Value added and non value added stps identification, FEMA process steps, Assemblish FEMS team, Completing FEMS template, Preparing occurance and detection tables, Graphical analysis - Data Stratification, Pareto Chart, Histogram, Box Chart, Scatter Diagram, 5 Why Analysis
UNIT 5: IMPROVE
The Improve introduction, Improvement strategy, Generating solution alternatives, Selecting best alternatives, Implement pilot phase, identify barriar to change, Solution implementation,
UNIT 6: CONTROL
The Control introduction, Mistake proofing (Poka-Yoke), Inspecting Vs. Mistake proofing, Discus eight type of solutions, Control chart, Run chart, process variation, Using MiniTab for plotting various charts. Developing and implementing control plan.
BENEFIT
- Gain sufficient understanding of Lean Six Sigma to be able to work effectively in improvement team.
- Learn to analyse and refine processes to improve efficiency and remove waste using Lean.
- Apply Six Sigma principles and techniques to reduce process variation and improve quality and consistency.
- Contribute to your continuing professional development.
- Add value for customers, employees and shareholders by minimising process variation and waste.
- Improve performance and reduce time scales for Lean Six Sigma projects.
- Reduced cost, improved efficiency, better resource utilization, more profitable organization
- Certified people demonstrate knowledge of Six Sigma. They are always in demand.
WHO SHOULD ATTEND
This course is designed for individuals from diverse organizational functions-operations, quality, logistics, finance, production, engineering and other staff functions. Participants are normally process owners or leaders and are well versed in technical aspects of their jobs and have worked on project teams.
Minimum Expectations for a Certified Six Sigma Green Belt
- Any Graduate or Professional can attend six sigma green belt training who wish to learn & Implement six sigma
- Future Managers including management students, Quality Assurance Engineers, Project Managers, Team leaders, Software Professionals, Practitioners, Software Quality Assurance team members and Senior Management who intend to implement and practice Six Sigma
- Any other professional members who are involved in research, innovations or consulting in process improvement practices.
EXAM
There is no prerequisite to do this course.
Exam Details:
- No.of questions: 100
- Exam Format: Multiple Choice & True or False questions
- Exam Pass Mark: 70% (70 out of 100 questions)
- Level of Qualification: Six Sigma Green Belt
- Electronic Devices Permitted: No
- Open Book: No
REQUEST FOR CALLBACK
Related COURSES
TRAINER
Trainer is a PEOPLECERT, EXIN, PECB, DMI, CCC, MILE2, IGC, APMG, BTC, BTA, GAQM & IGC accredited Trainer with over 25 years of experience in IT industry. Have trained more than 20,000 people in past 13 years. Almost every training batch has rated training delivery at 4.5+ on the scale of 1 to 5. Delivered training for global companies like Microsoft, Deloitte, JPMC, Barclays, Open Solutions, Oracle, Fiserv, Pepsi, Accenture and many other comapanies.
Trainer is a PEOPLECERT, EXIN, PECB, DMI, CCC, MILE2, IGC, APMG, BTC, BTA, GAQM & IGC accredited Trainer with over 25 years of experience in IT industry. Have trained more than 20,000 people in past 13 years. Almost every training batch has rated training delivery at 4.5+ on the scale of 1 to 5. Delivered training for global companies like Microsoft, Deloitte, JPMC, Barclays, Open Solutions, Oracle, Fiserv, Pepsi, Accenture and many other comapanies.
GALLERY
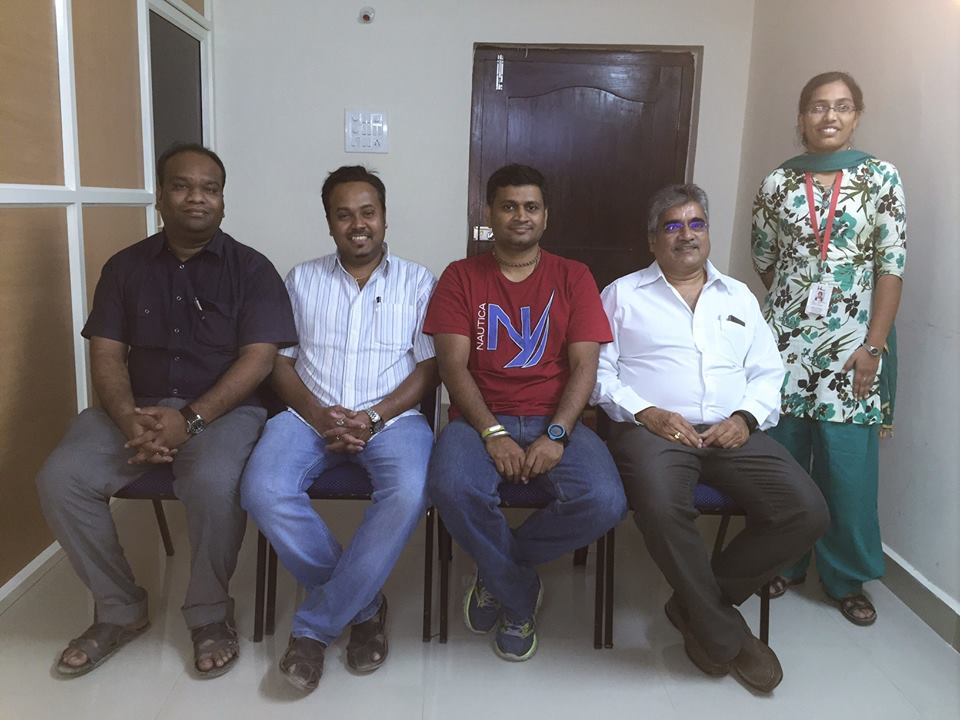
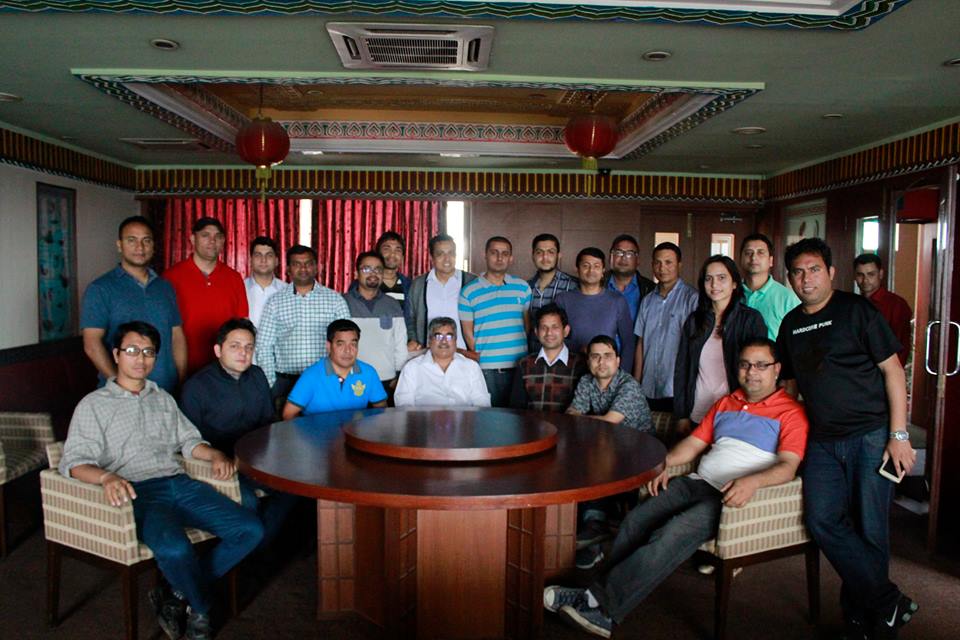
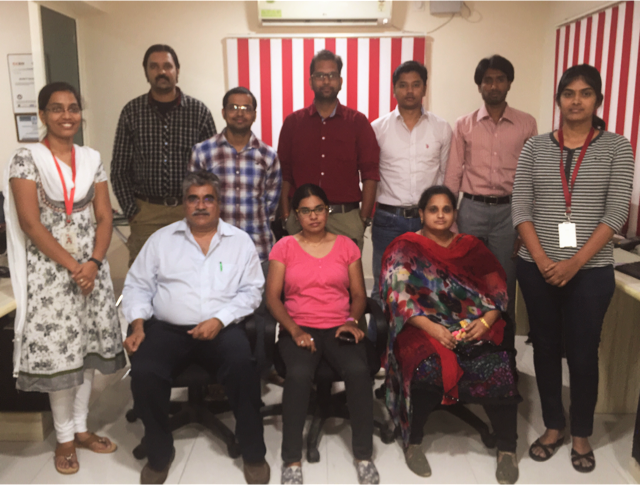
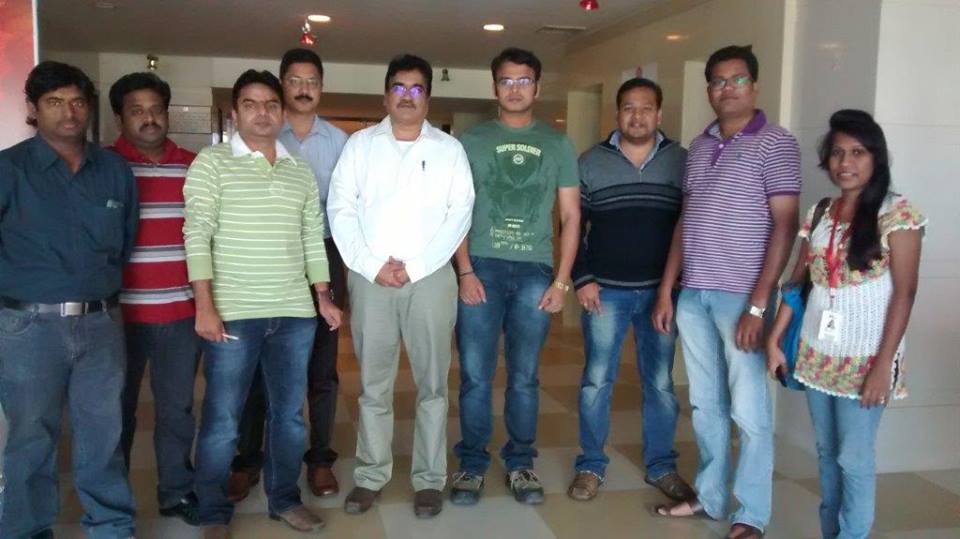
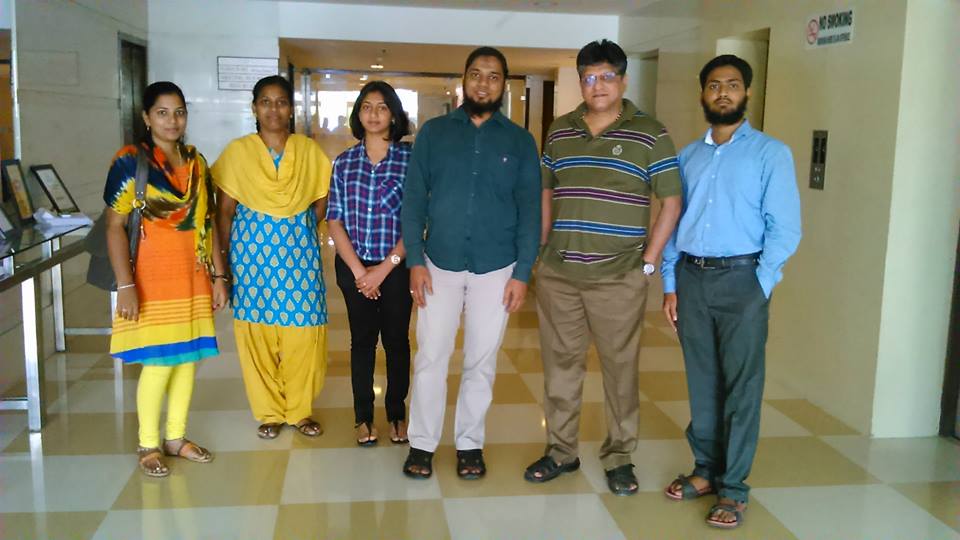
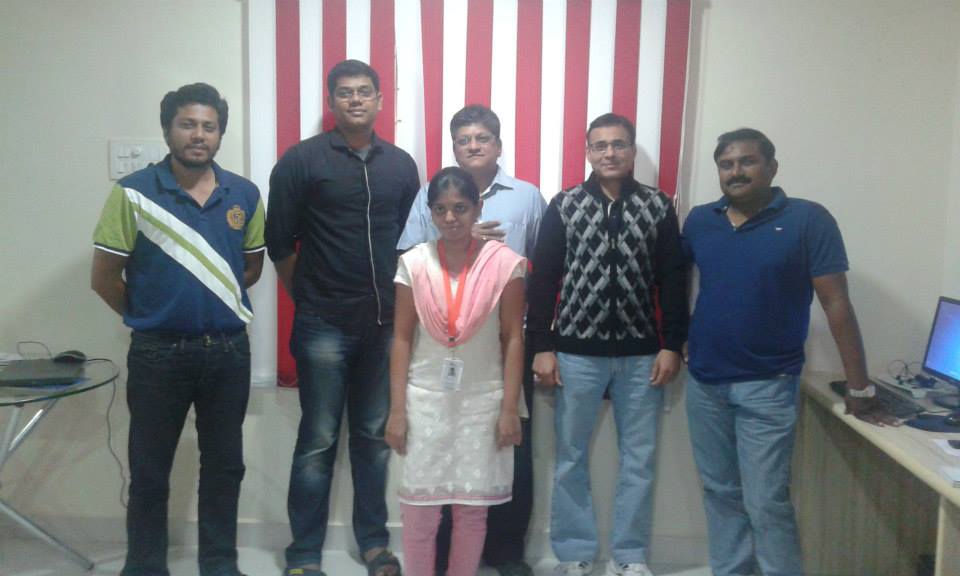
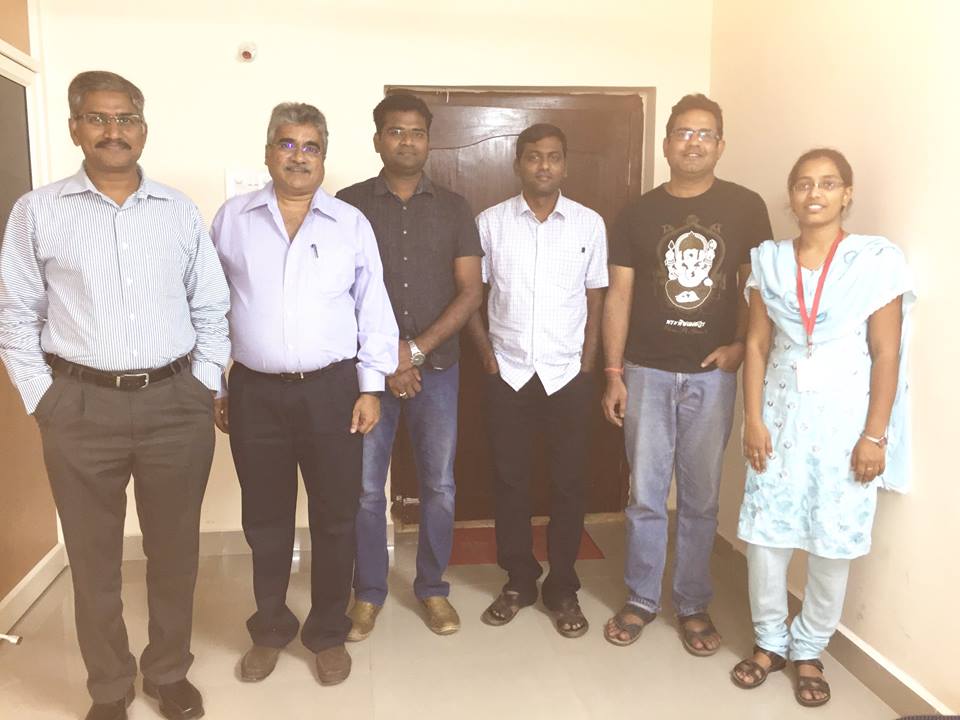
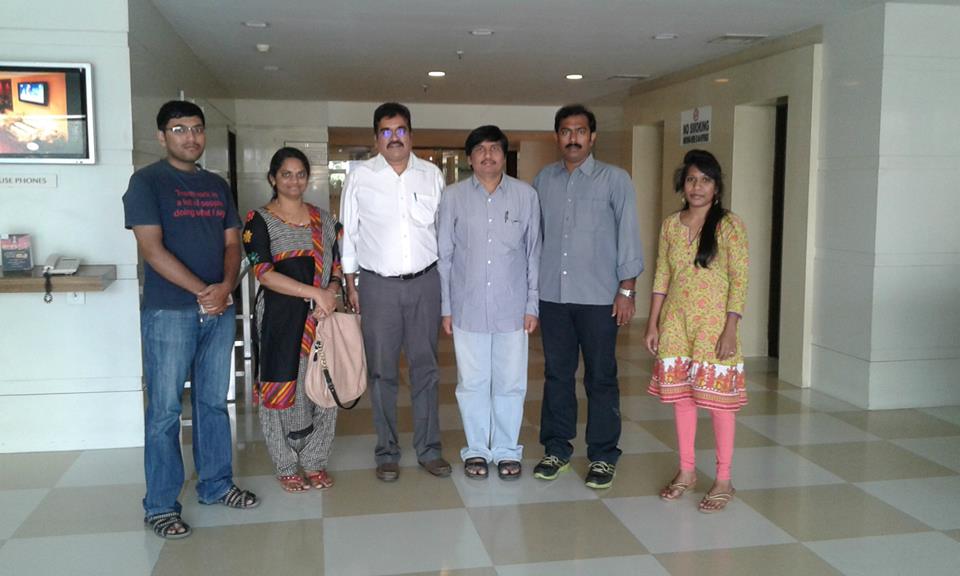
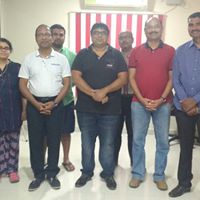
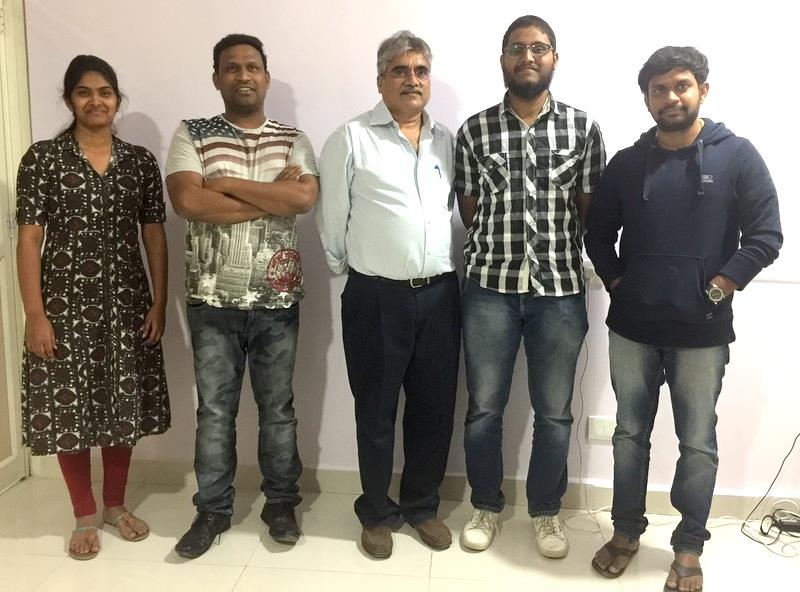
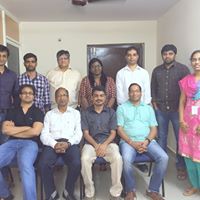
FAQ's
Choose Wiselearner in your journey
Reviews

Rajai Maini
Trainer is excellent in his subject knowledge and delivery. Highly recommended training institute.

Likhitha
United health group
Trainer is very good, has full knowledge as well as provided great examples which helped in understanding the concept well.